Manufacturing
Obtained certification for management systems related to quality and food safety
J-OIL MILLS has obtained ISO9001 certification (quality) and ISO22000 certification (food safety), which are international standards for management systems related to quality and food safety, at all of its production sites.
We manufacture our products under a thorough quality control system in order to create safe and reliable products.
In addition, the scope of ISO 9001 certification has been expanded beyond the production department to include business (marketing, etc.), R&D, and corporate departments, and all employees are working together to improve and enhance our operations, from product planning and design to the manufacturing process, quality inspection, inventory management, transportation and delivery, and the administrative departments that support these.
Our business (marketing, etc.), R&D, and corporate divisions obtained ISO 9001 certification in May 2019, and in February 2024, we unified our ISO 9001 certification with the production division.
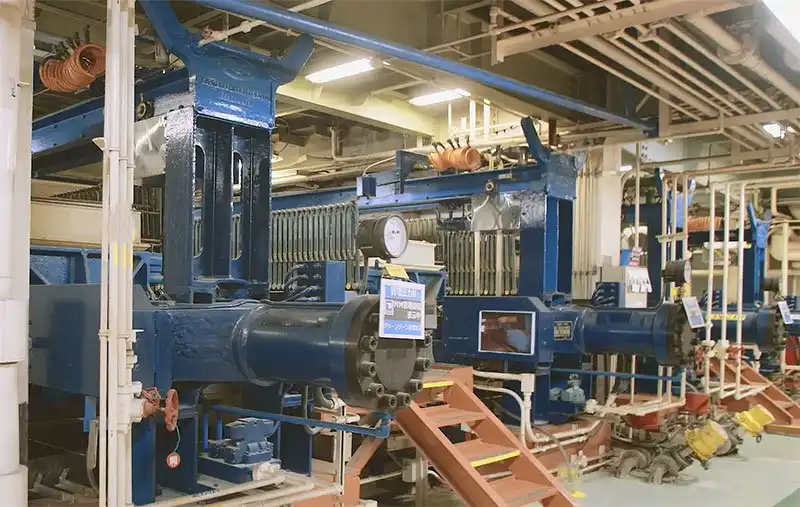
ISO9001 and 22000 certification status of each plant
Plant name | ISO9001 | ISO22000 | |
---|---|---|---|
(Certification date) | (Certification unification date) | (Certification date) | |
Chiba factory | March 2004 | February 2024 | June 2010 |
Yokohama factory | March 2004 | April 2010 | |
Shizuoka plant | April 1999 | May 2009 | |
Asaba factory | April 1999 | July 2018 | |
Kobe factory | November 2000 | February 2009 | |
Wakamatsu factory | July 2001 | March 2012 |
Initiatives to prevent foreign matter contamination
We take various initiatives in the manufacturing area to prevent foreign matter from entering our products.
Clothing in the production area
When entering the manufacturing area, employees must wear special work clothes, hats, masks, and shoes to prevent foreign substances such as hair from getting into products.
~Wear clean work clothes~
Wear clean, dedicated work clothes. The zipper is securely tightened all the way to the neck, and there are no gaps around the wrists or ankles. Change work clothes regularly to maintain sanitary conditions.
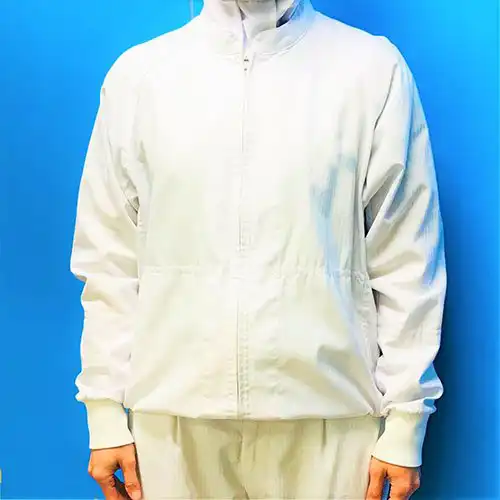
~Prevents hair from falling on employees entering the production area~
To prevent hair and other foreign matter from falling, a hooded sanitary cap is worn after putting on the hairnet. Wear a hat to prevent hair from sticking out, and tuck the cape into your jacket.
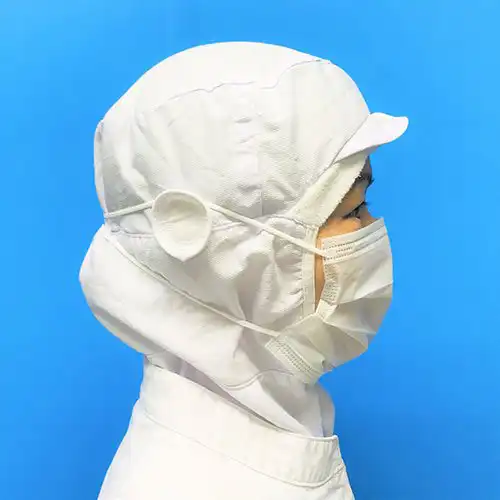
~Cover your mouth and nostrils to prevent droplets~
A mask that goes all the way to the back of your head and fits securely, completely covering your mouth and nasal passages to prevent droplets.
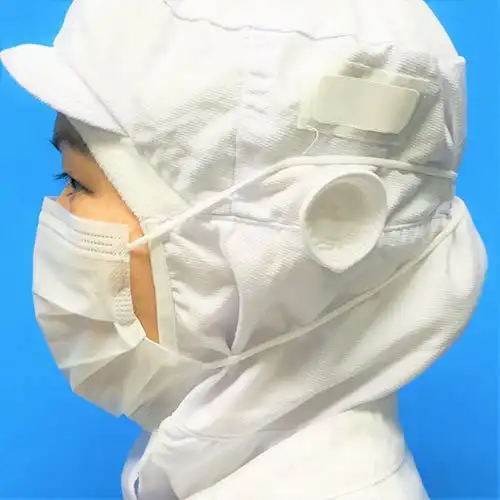
~Wear special shoes~
Wear special safety shoes designed with hygiene in mind. Before entering the manufacturing area, remove foreign objects from the soles of your shoes.
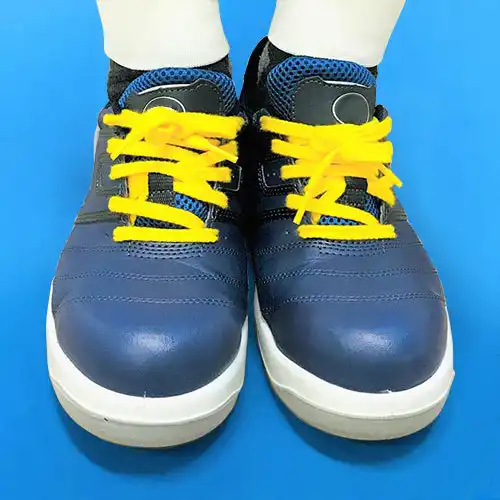
In addition, we have stipulated various items that are prohibited from being brought in when entering the room, and we do not bring in items that could lead to contamination.
This applies not only to employees, but to everyone who enters the production area.
Procedures for entering the production area
When entering the room, we follow established procedures to ensure that no foreign objects are brought in by using an adhesive roller, washing our hands, and passing through an air shower.
To maintain hygiene, the following steps will be taken when entering the production area:
Remove deposits such as hair and dust with an adhesive roller.
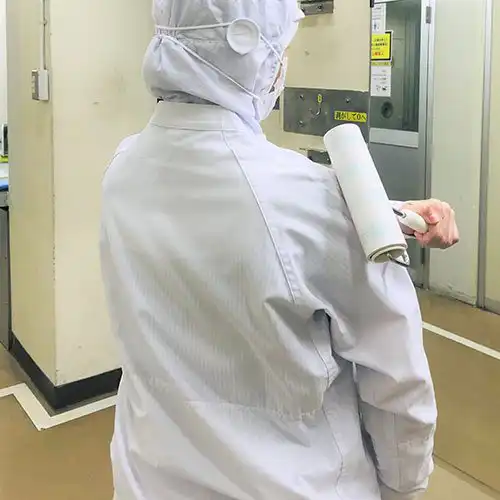
Clean with soap, dry with a hand dryer, and then disinfect with alcohol.
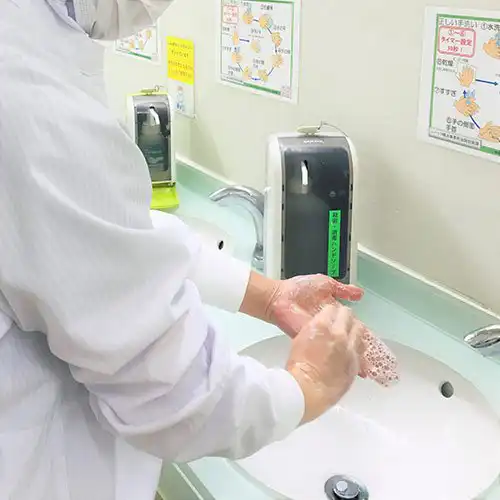
The air shower room blows clean air over your entire body to remove fine dust.
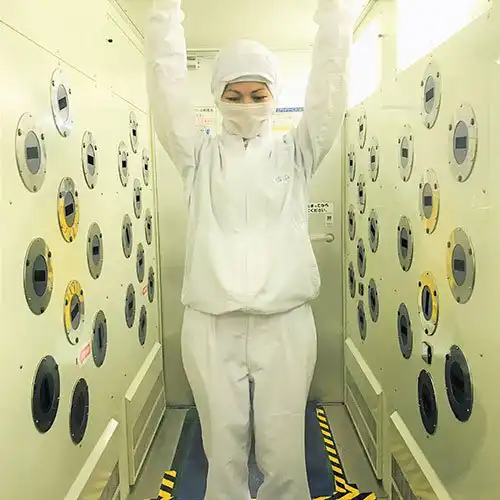
Product filling
On the filling line where oil is filled into containers, the products undergo automatic inspection using equipment such as image inspection and metal detection, and then are finally inspected by human eyes to ensure that no defective products are passed on.
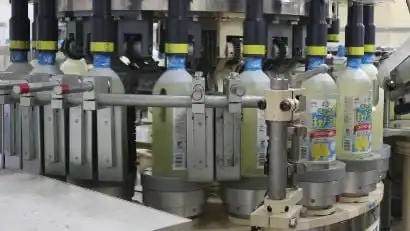
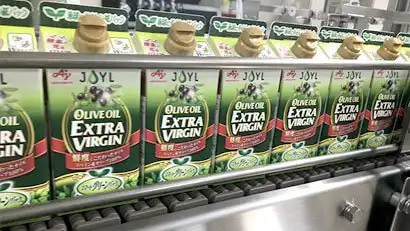
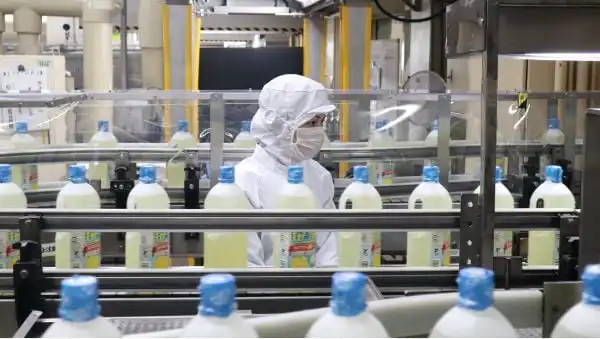